Inventory Control: Best Practices for Efficient Stock Management
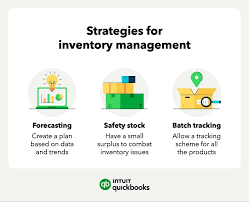
In today’s fast-paced business landscape, effective inventory control can be the difference between profitability and loss. Whether you’re running a small e-commerce store or managing a large-scale warehouse, having a solid handle on stock levels ensures smooth operations, customer satisfaction, and optimized costs. This blog explores the best practices for mastering inventory control, offering actionable strategies to streamline your supply chain and improve business performance.
What is Inventory Control?
Inventory control, also known as stock control, refers to the process of managing a company’s inventory of goods, tracking their purchase, storage, usage, and sale. The goal is to maintain optimal inventory levels that meet demand without overstocking or understocking.
It involves determining:
- What products to stock
- How much to stock
- When to reorder
- Where to store items
Efficient inventory control reduces storage costs, prevents loss through obsolescence or spoilage, and improves order fulfillment.
Why Inventory Control Matters
Poor inventory control can lead to serious consequences:
- Overstocking leads to the high holding costs or possible waste.
- Understocking can the cause missed sales backorders or frustrated customers.
- Inaccurate data causes poor forecasting, inefficient purchasing, and lost revenue.
In contrast, well-managed inventory:
- Improves cash flow
- Enhances customer service
- Reduces waste and losses
- Supports scalable growth
- Implement a Robust Inventory Management System
Manual tracking via spreadsheets is error-prone and inefficient. Adopting a digital inventory control system automates tracking, provides real-time visibility, and integrates with sales and procurement.
Key features to look for:
- Barcode scanning
- Real-time stock updates
- Forecasting and analytics
- Multi-location tracking
- Integration with accounting, CRM, and ERP systems
- Classify Inventory with ABC Analysis
Not all items are equally important. ABC analysis classifies inventory into three categories:
- A items: High-value, low-frequency sales (e.g., specialty equipment)
- B items: Moderate value and sales frequency
- C items: Low-value, high-frequency sales (e.g., office supplies)
This helps prioritize control efforts and allocate resources effectively, with tighter control over “A” items and relaxed oversight for “C” items.
- Set Reorder Points and Safety Stock
Setting minimum stock levels (reorder points) ensures replenishment before running out. Safety stock provides a buffer against supply chain disruptions or demand spikes.
To calculate reorder point:
Reorder Point = (Average Daily Usage × Lead Time) + Safety Stock
Regularly review and adjust based on demand fluctuations, seasonality, and supplier performance.
- Use FIFO (First-In, First-Out)
The FIFO method ensures older stock is sold before newer stock, which is crucial for perishable goods, cosmetics, or items with shelf life.
Benefits include:
- Reduced waste
- Improved quality control
- Accurate cost accounting (especially in inflationary times)
Organize storage to support FIFO by placing newer stock behind older stock.
- Perform Regular Audits and Cycle Counts
Physical stock should match system records. Conducting periodic audits — whether full inventory counts or more manageable cycle counts — ensures data accuracy and highlights issues like theft, spoilage, or data entry errors.
This method is less disruptive than annual counts and keeps data continuously accurate.
- Monitor Key Inventory Metrics
Track key performance indicators (KPIs) to gauge inventory health:
- Inventory Turnover Ratio: How often stock is the sold or replaced
- Days Sales of Inventory (DSI): Average days to the sell inventory
- Stockout Rate: Frequency of inventory shortages
- Carrying Cost of Inventory: Storage, insurance, depreciation, and opportunity costs
These metrics help identify inefficiencies and guide decision-making.
- Integrate Sales and Inventory Forecasting
Historical sales data combined with market trends and promotional calendars can forecast future demand. Integration of sales and inventory forecasting ensures you’re prepared for demand surges and seasonal changes.
Forecasting tools in inventory management systems analyze:
- Purchase history
- Lead times
- Market trends
- Customer behavior
Accurate forecasts reduce excess stock and prevent shortages.
- Optimize Supplier Relationships
Strong vendor relationships contribute to the smoother replenishment or better pricing. Evaluate suppliers based on:
- Lead times
- Order accuracy
- Flexibility
- Communication
Establishing backup suppliers and negotiating clear service-level agreements (SLAs) minimizes disruption risks.
- Embrace Just-in-Time (JIT) Inventory Control
Just-in-Time inventory control minimizes stock by receiving goods only as needed. This approach reduces holding costs or waste but requires highly reliable suppliers or precise demand forecasting.
Pros:
- Lower carrying costs
- Reduced waste
- Lean operations
Cons:
- Vulnerability to supply chain disruptions
- Requires strong supplier coordination
JIT is ideal for businesses with predictable demand and agile supply chains.
- Train Employees and Standardize Processes
Inventory control is only as strong as the people managing it. Training staff on proper handling, data entry, and system use prevents costly mistakes.
Standard operating procedures (SOPs) for receiving, storing, picking, and packing help maintain consistency, especially during scaling or high-volume periods.
Common Inventory Control Challenges
Despite best practices, businesses may face hurdles:
- Inaccurate forecasting due to market volatility
- Supplier delays affecting replenishment
- Stock shrinkage from theft or misplacement
- Software limitations in scaling or customization
Regularly evaluating your inventory control processes and being adaptable helps overcome these challenges.
Technology Trends in Inventory Control
Modern inventory control leverages emerging technologies:
- IoT (Internet of Things): Real-time tracking via smart sensors
- AI and Machine Learning: Predictive analytics and anomaly detection
- RFID Technology: Faster scanning and real-time stock updates
- Blockchain: Transparent supply chain records
These innovations enhance visibility, accuracy, and efficiency, giving early adopters a competitive edge.
Conclusion
Effective inventory control is vital for operational efficiency and long-term profitability. By leveraging technology, implementing sound strategies, and continuously monitoring performance, businesses can ensure optimal stock levels, reduce waste, and enhance customer satisfaction.
Whether you’re managing a retail store, manufacturing unit, or online marketplace, adopting these best practices will streamline your inventory processes and position you for sustainable growth. Take control of your inventory — and in turn, your business success.
Source: Inventory Control: Best Practices for Efficient Stock Management